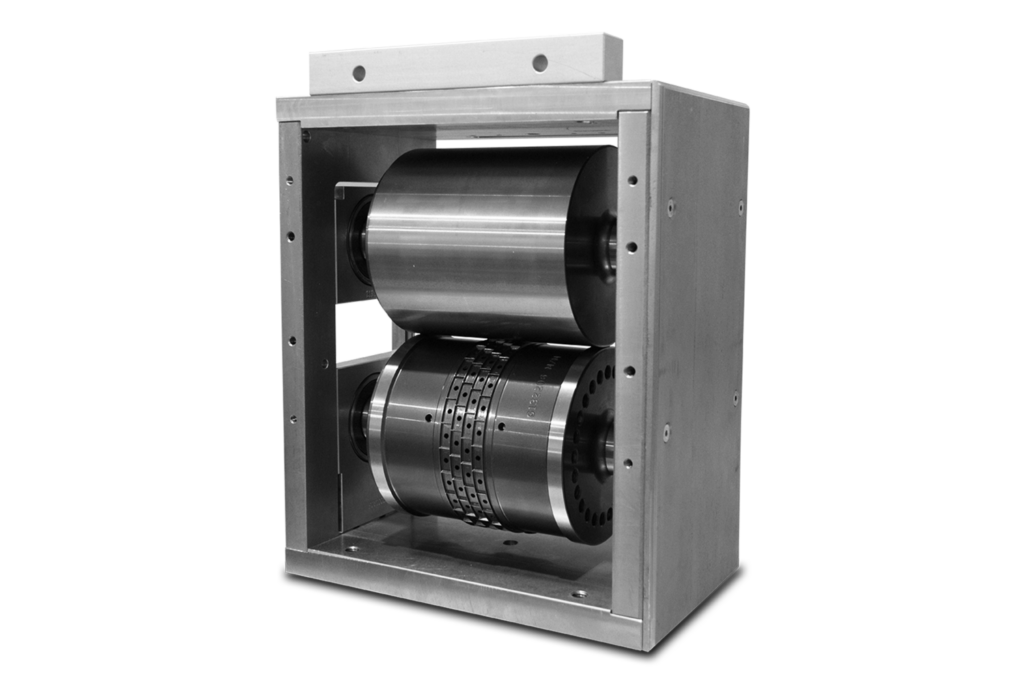
Rotary Die Module: Increase Production and Accuracy While Reducing Costs
A rotary die station is a critical component in manufacturing processes that require precise cutting, shaping or perforating of materials. By utilizing a cylindrical die, this technology enables high-speed, continuous production, making it indispensable in industries such as medical devices, packaging, labeling and flexible electronics.
How the Rotary Die Module Works
In a rotary die station, a continuous web of material — such as paper, film, foils, nonwovens, laminates or high-performance materials — is fed through the station into the rotary tooling. The rotary tool, often a cylindrical die with a cutting surface, creates the required profile or pattern. The die rotates in perfect sync with the material feed, ensuring precise cuts, creases or perforations according to the design specifications. This synchronization is essential for maintaining consistent quality and accuracy throughout the production process.
Types of Rotary Dies
Rotary dies come in different types, each tailored to specific applications:
Solid machined dies. These are machined from a solid tool steel bar, providing exceptional durability and precision. Their through-hardened tool steel construction allows for resharpening, offering years of reliable service and making them ideal for high-volume production runs.
Cut-off dies. These dies feature removable and replaceable blades, allowing quick changes to accommodate different materials or designs. Cut-off dies can cut or perforate depending on the specific requirements of the application, offering unmatched flexibility.
Advantages of Rotary Die Stations
Implementing rotary die stations in manufacturing provides several significant benefits:
- Modular design. These stations are easy to integrate into an existing inline process. They allow for the creation of various cut patterns, providing adaptability and seamless operation.
- High efficiency. The continuous nature of rotary die stations enables rapid processing speeds, significantly reducing production time and increasing throughput.
- Precision. Synchronized rotation between the die and material ensures highly accurate cuts and formations, maintaining tight tolerances. Servo-driven stations offer even greater accuracy, particularly for applications requiring precise cut registration.
- Versatility. Rotary die stations can process a wide range of materials and perform diverse operations, including cutting, perforating and creasing, making them indispensable across multiple industries.
Applications of Rotary Die Stations
The versatility and efficiency of rotary die stations make them suitable for a variety of applications.
- Bolt-on modules. Rotary die modules are self-contained units that can be easily added to existing processes. They integrate seamlessly and match the speed of your production line, making them an ideal solution for enhancing cutting capabilities.
- Unique shapes. Rotary dies can produce intricate, nested parts and creative designs at high speeds. Dies can also be engineered to cut to specific depths, which is particularly useful for laminations or multi-layered materials.
- Flexible materials. These stations excel in producing components with exact dimensions, such as medical devices, gaskets, seals and other precision-shaped parts.
Considerations for Implementing Rotary Die Stations
When integrating a rotary die station into a manufacturing process, it’s important to evaluate several factors, including:
- Material compatibility. Ensure the materials are suitable for rotary die cutting by considering the thickness, hardness and flexibility.
- Design complexity. Complex designs may necessitate specialized dies or additional processing steps, which could impact cost and production time.
- Production volume. High-volume runs benefit the most from rotary die stations due to their speed and efficiency. For low-volume or prototype runs, intermittent punches or other methods may be more cost-effective.
Achieving Precision and Efficiency
By adopting a systems approach and optimizing all cutting process parameters, you can achieve high-quality, dimensionally consistent cuts at high speeds. Rotary die stations are simple to bolt on and use, offering unmatched precision, efficiency and versatility across various industries.
Understanding your unique operation, we can demonstrate how rotary die technology can meet your needs, helping you make informed decisions about integrating this solution into your production process.
Contact us today to get started.